THE JOURNAL
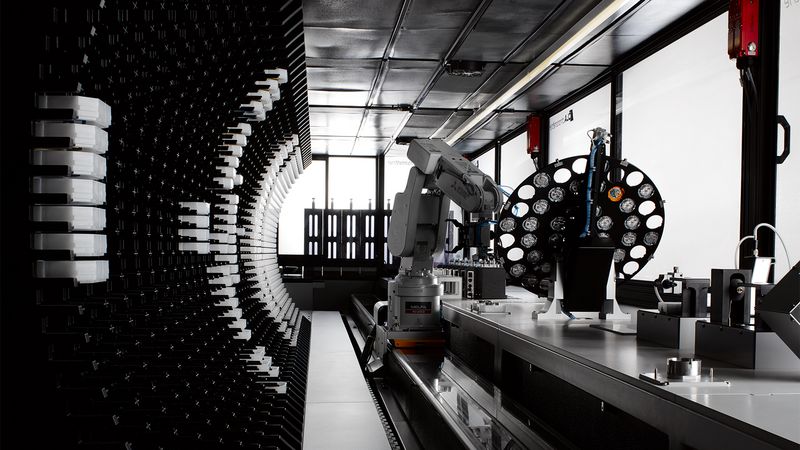
Production workshop at Panerai Manufacture site, Neuchâtel, Switzerland. Photograph courtesy of Panerai
“There is,” says Mr Max Büsser, founder of MB&F, “this sense that high-end watchmaking is all about some old guy with a loupe at a bench in an Alpine chalet, that it’s that traditional. There are elements of that. But it’s as much a high-tech industry of sterile laboratories as well now.”
Indeed, from the use of 3D printing in prototyping, as at Cartier, to the creation of a hairspring in carbon or silicon, at TAG Heuer or Ulysse Nardin respectively, recent years have seen brands innovate – in materials, construction, functionality – every bit as much as, say, car making or yacht building.
“That’s a new, more progressive vision for watchmaking,” adds Mr Büsser, “combining very old but also very new ideas in the same watch. What we’re now seeing is a more concerted effort to take mechanical watches forward.”
Here then, are some of the latest, biggest ideas in watchmaking tech from MR PORTER’s brand selection.
01. HYT’s mechanical light
“We like to mix traditional high-end mechanical watchmaking with the most advanced tech we can find,” explains HYT’s CEO Mr Gregory Dourde. “And that can mean taking inspiration from old problems.” Such as, for example, how to read a dial in the dark. Super-LumiNova works, but only for a time, and if the dial has been well exposed to sunlight beforehand. Chiming watches – the original after-dark timekeeping solution – is quaint but outdated, and incredibly demanding to produce. And battery-powered light isn’t right for a high-end watch.
HYT’s new idea? For its Flow collection, it has developed a tiny mechanical micro-generator of rotating magnets – shielded from the movement, of course – linked to a dedicated hairspring. This micro-generator powers a cluster of tiny LEDs, arranged so as to distribute light across the entire dial. The wearer provides the energy – each press of a pusher provides enough to illuminate the dial for two seconds. Doing so creates an alternating current though, and LEDs work on direct current – so, in fact, they actually flicker on and off, but at such a rate (1,000 times per second) that the human eye can’t detect as much.
“Generating electricity with a copper coil and magnets isn’t a new principle, of course – it’s been around since Faraday,” says Mr Dourde. “The real challenge was the miniaturisation. But we also like the idea of putting those LEDs under a dome of diamonds, as we’ve done in one model. Diamonds need light to come alive, after all.”
02. Panerai’s wonder material
“We’re always looking for new materials that might improve a watch’s performance or reliability, but the aesthetic of the material is very important, too,” says Mr Alessandro Ficarelli, Panerai’s product development director. He’s speaking of what he calls “the world premiere” this year of Fibratech, a composite polymer material based on basalt rock fibres that’s super strong, 55 per cent lighter than titanium but also immune to corrosion, making it ideal for a Panerai Luminor diving watch.
Indeed, Panerai has a globetrotting team focused on the hunt for new innovations to use in its watches, and found Fibratech in competition yacht racing – the aeronautical and medical industries are good places to look, too. Fibratech is limited – it’s expensive and can’t be produced in large quantities. “And,” Mr Ficarelli says, “we added some minerals to Fibratech to improve its look – and the colour it has is unlike anything in the market now.”
Certainly not all materials make the grade for watchmaking – Panerai experimented with recycled carbon fibre but in the end could only make it work for use in dials. “Steel and precious metals will continue to dominate watchmaking, with some bronze and ceramics,” says Mr Ficarelli. “But the next big challenge for the industry will be the much greater use of recycled materials.”
03. Ressence’s automatic crown
We’re so used to automation, to our devices minimising the hassles of their use, that Ressence founder Mr Benoît Mintiens decided to see if he could do the same for the watch crown. The result is his Type 2 watch’s e-Crown. Put your watch down and it stops running. Pick it up, no matter how much later, and the watch – with a gentle tap on the glass – automatically re-sets to the correct time and starts running, no winding required.
This has been achieved by the development of a tiny electro-mechanical system, powered by an equally tiny photovoltaic-powered battery, all of which sits alongside but communicates with the entirely mechanical movement. Somewhere in there among the almost 500 parts is also a tiny camera that reads a coloured disc that allows the watch to set itself according to your time zone of choice. This has taken four years of trial and error.
“It’s like having an automatic gearbox in your car. Your car still has gears but the car changes them for you. It’s convenient and more efficient, too,” says Mr Mintiens. “You could remove the e-Crown component and the watch would work perfectly fine. But I think such advances are important – if you’re going to get a younger generation interested in mechanical watches then you have to speak their language. You have to make the way mechanical watches work more relevant without losing their emotional appeal.”
04. MB&F’s coding-influenced calendar
The first perpetual calendar timepiece was a pocket watch in 1762. The first time this mechanism – which correctly displays the correct date even allowing for leap years, right up until the end of the century – appeared in a wristwatch was in 1925. And since then this really rather special complication has advanced, well, hardly at all.
“In fact,” says Mr Büsser, “perpetual calendars generally just don’t work well. They jam, or owners force them and they break. But then it effectively works by pushing the system to do what it doesn’t want to do. There’s a reason why they’re dubbed ‘boomerang’ watches – because they spend their life going out from the workshop, then back to the workshop.”
Until five years ago, when self-taught watchmaker Mr Stephen McDonnell suggested a solution to Mr Büsser: what is, in effect, a mechanical processor with a coding module of variably sized cams, which is set on 28 days as a default, rather than the traditional 31. On the 25th of every month, it tells the Legacy Machine’s movement what to do at the end of that month (ie, whether to reset at day 28, 30 or 31). Add in a retrograde system for the end of each month, greatly reducing the strain on the mechanics, a clutch that prevents the kind of damage perpetual calendars are often subjected to by their owners, and you have the first major update of this complication in a century. This summer MB&F went one better and, thanks to the development of a groundbreaking gasket, made its Evo edition waterproof, too.
“It’s all really such a simple idea that it’s a wonder nobody thought of it before. It’s one of those where you say, ‘Fuck, why didn’t I think of that?’” laughs Mr Büsser. “But advances in technology are so often just about looking at engineering problems in a more lateral way.”
05. Piaget’s integrated case
It’s not, Piaget’s Mr Balthasar de Pury admits, a new idea. The humble, though quite genius, Swatch watch got there first – making the quartz movement, usually tucked away inside a case, instead part of the case. In doing so, in theory, it met a fundamental tenet of engineering – saving on the number of parts, thus reducing unnecessary complexity, and streamlining production. But to do that in metals, and with a mechanical watch, would be another thing (Swatch’s solution was also effectively impossible to service; any mishap meant throwing the movement out and fitting a new one). And Piaget wanted to go further, integrating the caseback, mainplate and bezel. But then Piaget was setting about making the world’s slimmest mechanical watch – just 2mm deep.
“We knew we had to get rid of some components, and then came the idea of fusing them together – the more layers we could lose the better,” says Mr de Pury. “It sounds like it should make for a process that’s simpler, but it turns out this has been like making a high complication.”
Piaget’s solution, which has won it five patents? Machining the barrel directly into the case, and replacing the hour hands with a rotating disc. It was not a solution exactly rushed to; in manufacturing terms it’s high risk, since a mistake in making one part costs much more than that one part. Even polishing at the end could prove fatal to the watch. And, dealing with tolerances of 0.12mm, engraving was certainly out. Piaget decided it had reached the limits in working in gold and switched to using very hard cobalt for its Altiplano Ultimate Concept – so hard that all tools required to work it also had to be developed from scratch.
“The whole project was only meant to result in a single concept watch, which is one thing. But making that into a wearable watch, made-to-order, has been another altogether,” Mr de Pury adds. “Still, we had quite some fun working it all out.”